
CAD wORK
JET ENGINE




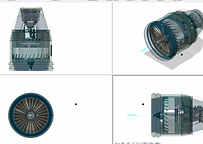
-
As a part of my side project I designed and modeled this Jet engine using concepts of Reverse Engineering.
-
Used tools like FUSION 360 for modeling, GRABCAD for calculating the center of masses of each component, and EAGLE for PCB design.
-
The assembly includes 72 components and 21 subassemblies, this project took 2 weeks to be fully completed.
​
BUSHING ASSEMBLY





-
On my first co-op, I converted 2-D blueprints of a medical part into a 3-d model.
-
The assembly consisted of 4 components- Tube, bushing, outer capsule, and inner capsule.
-
I used grabCAD to find the center of gravity and mass and used Fusion 360 for the modeling part.
-
While testing the model, it was 95.66% accurate to the 2-D blueprint.
CUSTOM COMPOUND
GEAR



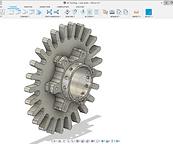

-
As a part of a project in my co-op, I redesigned a compound gear to meet the requirements.
-
Used AutoCAD and GrabCAD to make a 2-D blueprint and calculate the center of mass and material requirements.
-
Converted 2-D sketch to a 3-D model using Fusion 360 DESIGN, and generate a tool path and G-code using Fusion 360 MANUFACTURE.
PLANT ASSEMBLY





-
Made a 2-D layout, and a 3-D model of a nuclear plant using AutoC AD and Fusion 360.
-
All dimensions are with proper constraints.
​
PHONE STAND





-
Designed and modelled this phone stand using solid works.
-
Used grabCAD to calculate material volume and Determined the centre of gravity and used it to make modifications in the design.
-
3-D printed the stand using a Modix- Big 60 V3 printer.​
ANTI-ROTATION PIN
ASSEMBLY





-
Worked with the design and engineering team at my co-op and 3-D modelled a anti rotation pin for Rolls-Royce Turbo jet engine.
-
Used Fusion and AutoCAD to constrain all sketches and check all the measurements as this Assembly had tight tolerances.
-
The model accuracy reduced time of the CNC programming team by 20% .